Hybrid photonic integration leverages the advantages of diverse material platforms, providing enhanced performance and flexibility compared to traditional monolithic approaches. This is particularly beneficial for multi-chip architectures, where individual components can be independently optimized and tested.
However, assembling these systems typically demands high-precision alignment and adaptation of optical mode profiles, making it both complex and costly.
Our partner innovative approach overcomes these challenges using in situ 3D-Printed Freeform facet-attached beam-shaping elements. This technique allows precise adaptation of vastly dissimilar mode profiles while maintaining alignment tolerances that are compatible with cost-efficient passive assembly techniques.
High-Efficiency 3D-Printed Freeform Beam-Shaping Technology
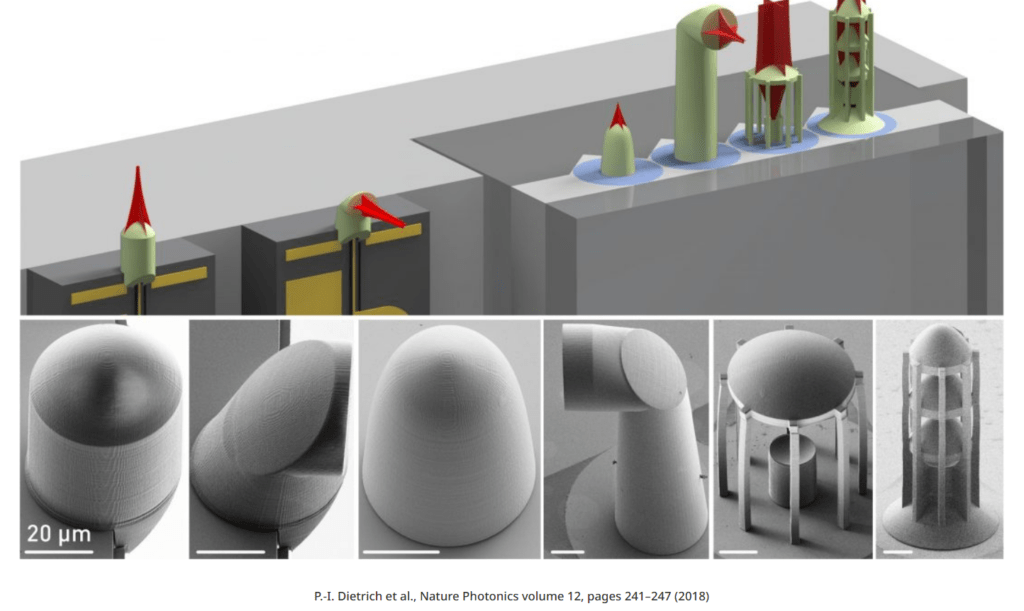
As demonstrated in P.-I. Dietrich et al., Nature Photonics volume 12, pages 241–247 (2018), our 3D-Printed Freeform optics technology achieves coupling efficiencies of up to 88% between edge-emitting lasers and single-mode fibers. Additionally, our partner have successfully implemented printed freeform mirrors, which dynamically adjust beam shape and propagation direction, as well as multi-lens systems for beam expansion.
This groundbreaking advancement paves the way for automated photonic multi-chip assembly, delivering superior performance and versatility.
Our partner 3D-Printed Freeform optics technology supports a wide range of optical components and features:
1. Compatible Components
- Laser sources (DFB and other types)
- Photonic Integrated Circuits (PICs): SOI, SiN, InP, LiNb
- Fiber arrays: SMF, PMF, and MMF
- Photodetectors: PIN and APD diodes
2. Standard 3D-Printed Freeform Optics
- Focal lengths up to 5 cm and mode-field diameters from 1.2 μm to 80 μm
- Mode-field converters for enhanced beam shaping
- Total-internal-reflection mirrors and angled facets
3. High-Performance Coupling
- Laser-to-PIC interface losses: 0.7 dB to 2.5 dB
- Back-reflection below -30 dB
4. Precision Alignment
- ±1.5 μm for single-lens components
- ±20 μm for beam expanders
5. Broad Operating Range
- Wavelength compatibility from 530 nm to 1650 nm
6. Fast Fabrication
- <60 seconds, depending on the optical model
7. Exceptional Reproducibility & Accuracy
- Mode-field diameter (MFD) variation: σ < 0.2 μm
- Shape accuracy: ±100 nm
- RMS roughness: <10 nm
8. Rigorous Environmental Testing
- 4000+ hours at 85°C / 85% RH
- 250+ thermal cycles (-40°C to 85°C)
- Reflow soldering (3 cycles at 270°C)
- Vibration resistance: 20g (all axes)
9. High-Power and Cryogenic Operation
- >1W @ 1550 nm
- 4000 hours @ 100mW on DFB facet
- >10 cryogenic cycles from 4K to room temperature
Conclusion: The Future of 3D-Printed Freeform Optics
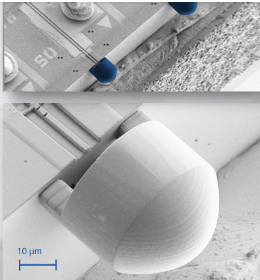
Our partner 3D-Printed Freeform beam-shaping technology is revolutionizing photonic device integration. By combining precision optics with high-efficiency passive assembly, this innovation enables seamless coupling, high-speed data transmission, and superior optical performance across various photonic applications.